要員の生産性やスキルは不確実です。よって、マネジメントの方針は人の不確実性を除去するのか、人のスキルと生産性向上を図るのかに分かれます、またはその両方の湯法をとることになります。人の不確実性を除去する1つの方法がマニュアル方式です。マニュアルが完備していれば、要員を交代することは簡単にできます。しかし、マニュアル方式による、業務成果は明確で、現実的なものに限定されます。一方、人のスキルと生産性向上を図る手法では人の管理が難しくなります。しかし、要員の業務成果は期待を超えることもあり、期待を超える業務成果は期待以上の利益をもたらすこともあり得ます。
要求仕様分析
要求仕様分析は事業計画を支援する。例えば、プロジェクトを計画通りに進めるためには、適切な計画が必要である。具体的には、プロジェクトには、適切な開発仕様の作成と費用設定が必要となる。そこで、適切な計画立案に向けて、要求仕様分析を提案する。要求仕様分析にはコストシェアレート分析と要求仕様関係分析があり、コストシェアレート分析はそれぞれの要求仕様が占める費用割合を分析する。そして、コストシェアレート分析は費用的に見た要求仕様の重要性を評価する。図1にコストシェアレート分析の例を示す。本例では要求仕様NO13の開発費用が最も大きな開発費用を占めており、更にインターフェース関連費用の開発費用が大きいことを示している。更に、図2は要求仕様の改訂に伴う費用の増加を示しており、コストシェアレート分析により、仕様改訂に伴う費用予測が可能となる。図3は要求仕様関係分析の例を示しており、本例は要求仕様の1と2が基本仕様であることが示されており、要求仕様の1と2は詳細な検討が必要なことを示している。



イノベーション製品とは
イノベーション製品とは以下の条件を満たすもの
(1)製造者が価格を決められること
(2)製品機能が消費者の視界にないこと
プロダクトイノベーションとは
イノベーション的な製品は以下の2つがポイントです。1つは客の視界になく、製造者が価格を決定できること。2つ目はマーケットの大きさは変わらないので、他のマーケットから資金を取ってくる製品であることです。
マネジメントと管理
世の中には、様々な課題解決のためのプロジェクト活動や日々の各種業務が進められており、業務の進め方として管理とマネジメントがある。管理とは、何か対象物や管理値を制御することであり、英語ではControlである。一般的に、管理は対象物や管理値が管理上限と管理加減以下にならないように制御することである。例えば、図1の管理が示す様に、残業制限が40時間の時、各要員の残業時間が管理値以内になるように、管理課長は定時退社日にはオフィスの明かりを消して回ったりする。一方、マネジメントは到達目標を認識して、持てる資源を最大限に使用して、より早く、そしてより効率的に目標を達成を目指す。従って、マネジメントは目標を理解して、目標に至る最短道を進むことが必要である。例えば、図2に示す様に家から学校までの最短道を探すのと同じである。また、道の探し方はスタートから始めるボトムアップではなく、目標から始めるトップダウンの方が効率的である。そこで、マネージャには多くの経営資源を動かすこと、そして経営資源を効果的に動かすことが求められる。例えば、図1のマネジメントの、その他の経営資源として、信頼関係、取引関係、販売や購入ルート、馴染みの商社やネームバリューがある。そこで、優秀なマネージャになるには、動かせる経営資源を増やすことと動かし方を学ぶことが求められる。
軽視例えば、プロジェクト遂行に於ける目標達成を不安定にする要素はス


レビューやレジメを要約して検索する
観光地や製品に関する多くのレビューを読むのは困難であるため、自動要約して検索することが求められます。また就職や再就職に関する自己アピール文やレジメを担当者が読むのは困難であるため、自動要約と検索が求められます。
購買行動は全方位価値比較
ビジネスでのコンペチターは同じフィールドにいるとは限りません。人は属性の異なるものを比較することができます。たとえば図1にあるように世界旅行と中古の軽自動車の価格が100万円程度で同じであるとすると、購入に当たっては比較することができます。人が属性の異なるものを比較できる理由は図1のレーダチャートにあるように人は旅行の楽しさ、記念度と車の利便性を比較できる能力をもつ事にあり、属性の異なるものを比較するの能力は車と旅行の価値順位を自由に入れ替えることのできる空間上に車と旅行が配置されていることにあります。
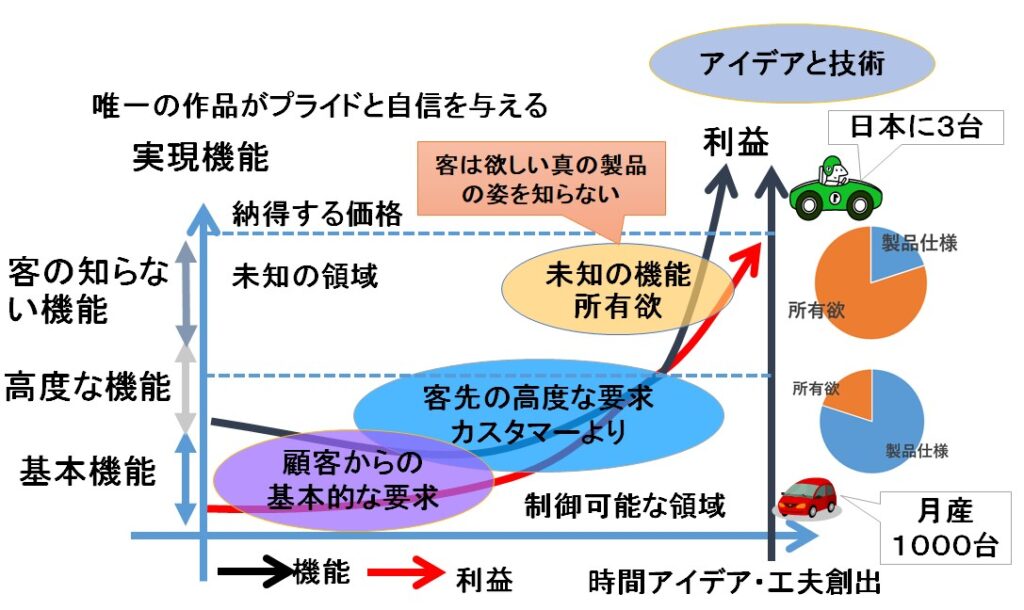
図1価値と利益
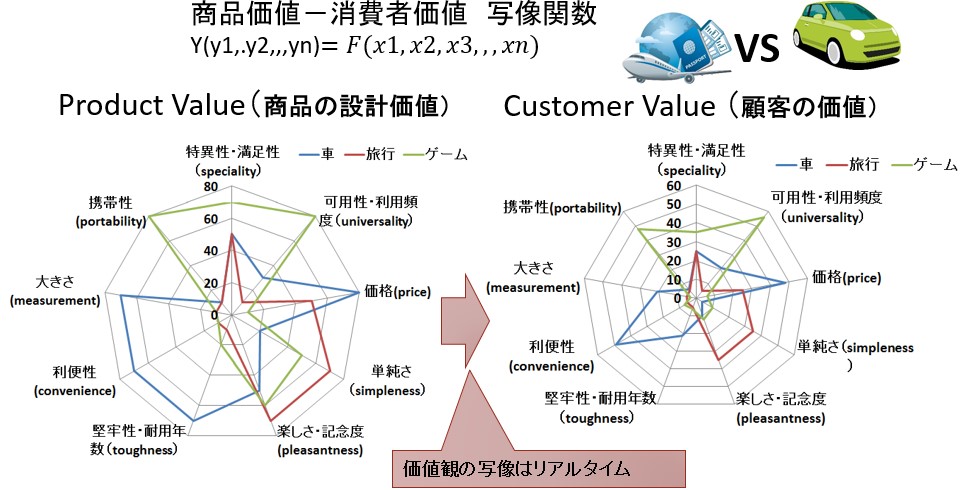
図2全方位価値評価
意味圧縮と文書要約
3秒ルールインテリジェンスは文章の意味解釈を行い、行動情報を取り出すことを目指しています。次のデモンストレーションでは入力した文章の要約を行います。ただし、開発中ですので特定な分野のみの対応となります。
文書要約デモンストレーション(開発中)
以下のサンプル文を入力して見てください。
呼子名物のイカは、透明でとろけるような舌触りで、きれいです。甘みもあり、刺身は最高です。しかし、時期と時間によってはイカが小さいので残念なことがあります。下足は後で天ぷらにしてもらうと2度楽しめます。でもてんぷらには少し時間がかかります
品質はスペック
品質とは何か、品質とはある人には壊れないことであり、ある人には安いことであり、製造者と顧客の立場の違いにより異なる。そして、品質は必ずしもユーザの立場で考えられている訳ではない。一方、工場の品質とは製品が製作精度に入っていることであり、ばらつきがないことである。製品にばらつきがあると消費者が払う対価に対して製品の価値が保証されていないことになる。従って、工場における製品の品質とは、ばらつかないことであり、必ずしも消費者の使い勝手が良いものではない。通常、図1に示す様に製品はスペックを満たす範囲でコストダウンが図られる。コストダウンの代表的な考え方としてリーンプロダクションシステムがあり、主なコストダウン手法に安い材料や安い部品を使うこと、加工が簡単になるように設計すること、人件費の安い所で作るがある。そして、製品のばらつきを減らして製品の価値を保証しようとする手法が6σである。

(1)リーン生産方式:lean product system
マサチューセッツ工科大学の国際自動車問題研究計画で指摘されている無駄のないスリムな生産方式で、具体的には,トヨタなど日本の自動車メーカで一般化している労働力、在庫、製品開発期間、工場スペースなど企業活動の中使用資源量、欠陥を減らす手法で、多様化する顧客ニーズに対応するシステムである。代表的な活動はムリムラムダの排除がある。
(2)6シグマ(シックスシグマ)
欠陥を減らすための品質管理手法であり、米国モートローラから始まった活動である。シックスシグマとは生産やビジネスにおけるエラーや欠陥を100万分の3~4の確率以内に抑えるシステム・プロセスを構築することを目的とした経営・品質管理手法のことである。
課題解決の課題は客先の課題
ビジネスはループであり、お客にはお客があり、組織の中でも他部門の人はお客さんである。そこでお客さんと良い関係を築くためには、客の客の課題解決を図ることが必要である。